By HARRY J. LUBITZ,
CSI, CDT, IIBEC,
United Gilsonite Laboratories
Did you ask the exterior of your structure… “Should I Breathe?”
Breathability of exterior coatings seems to be a subject I am questioned about weekly.
During the past several decades, exterior paint manufacturers have been touting the “breathability” of their products and how this is essential for water management with regards to the exterior envelope of a building.
They have trained their sales personnel to extoll the virtues of breathability and how it allows water vapor to escape from under their film-build coatings.
Hogwash . . . poppycock . . . and other naysaying terms.
We’re different in Florida and the movement of water vapor through an exterior envelope depends on where you live.
Building scientists will school you on the placement of vapor retarders (non-permeable layers or elements of the exterior wall system).
The warmer the climate, the more you push your vapor retarders to the exterior of the envelope. And vice versa for colder climates. That’s why you have a poly-film or faced insulation on the warm side of the wall if you grew up back north (before migrating south).
So why do paint manufacturers preach breathable coatings in Florida?
First, they choose not to accept building science.
If there is 85% relative humidity on the outside of your structure in sub-tropical Florida, and 55% relative humidity on the inside of your structure, what is the direction of the water vapor drive?
Outside to Inside!
Sorry, you can’t change physics.
Matter will move from an area of higher concentration to an area of lower concentration through a membrane to reach equilibrium. Consequently, water vapor trapped behind paint will want to move inward, and more water vapor on the outside of the paint will also want to move inward across the breathable paint film.
Yes, “breathable” paints in Florida pass water vapor. And the more breathable they are — or permeable — the more water vapor they will pass into the structure.
For example, a typical film-build paint coating is about 20 perms. “Perms” is the standard measure of permeability and usually measured with two coats applied to an ASTM Standard test. Any coating more than 10 perms is classified as “fully permeable”.
A 20-perm paint will pass about 33 ounces of water through one square meter of wall surface over the course of a year.
That’s a lot of water, and the building HVAC system will need to be sized properly to remove all that water.
Second, paint manufacturers tried to address a problem with stucco and masonry wall surfaces.
Generally, these surfaces crack over time and paint manufacturers discovered how to increase the elongation of paint films in the 1950s to “bridge the cracks” and reduce cracking and peeling complaints.
They coined the term “elastomeric” for this new class of products.
The unfortunate outcome in Florida was that the breathable coatings let moisture in rather than out, and the increased elongation of these coatings formed ”balloons” of water under the paint films.
So, what was the paint manufacturers’ solution? Make the coatings even MORE permeable. And then the painters, squeezed by the builders and GCs to reduce cost in a competitive bidding environment, starting applying even less paint . . . making the coatings even MORE permeable.
Now we have a scenario that the paint is so thin and breathable that the paint films are passing three times more water vapor into the structure, failing to meet wind-driven rain standards, and wearing out after a few years.
The HVAC systems then struggle to keep the interior of the structure dry, forcing the user to run the systems for longer periods of time, expending more energy and reducing the life span of the HVAC systems.
To break this vicious cycle, I recommend the use of non-breathable waterproof coatings over stucco and masonry in Florida.
Non-breathable waterproof coatings in Florida have become a popular option for owners looking to protect their structures from the elements. These coatings provide a barrier against moisture, wind-driven rain, hurricanes, and other elements that can cause damage to a structure over time.
One of the primary benefits of using non-breathable waterproof coatings is their ability to protect structures from water damage due to moisture buildup within a structure.
Non-breathable coatings act as a barrier, preventing moisture from entering the walls, slab/foundation, or other areas of the structure. This not only helps to prevent water damage, but it can also help to prevent the growth of mold and mildew, which can be harmful to both your structure and your health.
Back to our physics equation . . . since the vapor drive is inward, there is no need for a breathable exterior coating. Non-breathable waterproof coatings are generally less than 1 perm – or classified as “semi-impermeable”. This type of coating will pass only about 1 ounce of water vapor over one square meter of wall surface during the course of a year.
There are several different types of non-breathable waterproof coatings available, each designed to meet specific needs and requirements.
Some of the most popular options include acrylic latex, silicone, polyurethane, and epoxy coatings. Each of these coatings has its own unique benefits and drawbacks, so it’s important to carefully consider your specific needs and requirements when choosing a coating for your project.
There are several advantages to using an exterior non-breathable waterproof coating over stucco or masonry in Florida. These include:
• Improved Moisture Resistance: Non-breathable waterproof coatings provide a barrier against moisture, which is particularly important in Florida’s humid climate. This helps to prevent moisture from entering the walls of the structure, reducing the risk of water damage, mold and mildew growth, and other moisture-related problems.
• Enhanced Insulation and Energy Savings: Many non-breathable waterproof coatings are designed to provide additional insulation to your structure, which can help regulate temperature and reduce energy costs.
Reduced need for internal moisture and humidity removal can increase the lifespan of HVAC systems and reduce energy costs.
• Increased Durability: Non-breathable waterproof coatings are often more durable on stucco or masonry, and are better able to withstand the elements, such as wind, rain, and extreme temperatures.
This can help to extend the life of your structure and reduce the need for costly repairs.
• Low Maintenance: Non-breathable waterproof coatings are typically low-maintenance, requiring only occasional cleaning to keep them looking their best; since they are also usually thicker coatings, they tend to wear longer.
• Improved Aesthetics: Non-breathable waterproof coatings are available in a range of colors and finishes, allowing you to choose a coating that complements the style of your structure or match existing finishes.
In conclusion, there are several advantages to using an exterior non-breathable waterproof coating over stucco or masonry in Florida. Those advantages include improved moisture resistance, enhanced insulation, increased durability, lower maintenance, and improved aesthetics. When choosing a coating for your project, it’s important to consider your specific needs and requirements and to choose a coating that is right for your budget.●
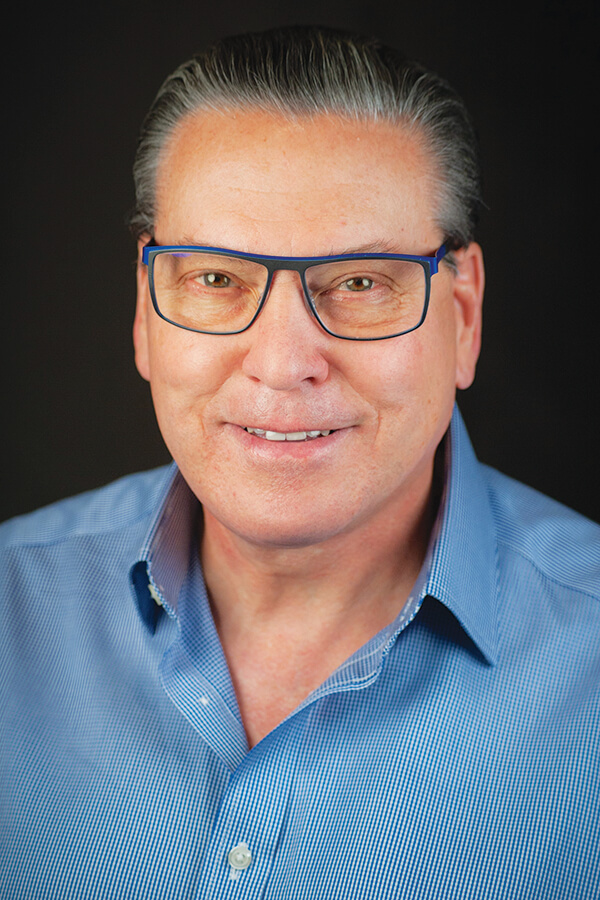
Harry Lubitz is an Architectural Consultant and Cold-Fluid Applied Waterproofing Specialist. Contact him at harry.lubitz@ugl.com.